The Feasibility Study: From Prototype to Mass Manufacturing
As the healthcare industry continues to advance, the importance for feasibility will only grow. As we have learned, the coming years will demand solutions that are not just innovative but practically attainable, and the integration of medical devices with wearable technology is poised to reach new heights. Custom medical electrodes designed for seamless integration with wearables will play a pivotal role in providing continuous, real-time health monitoring.
With an increasing focus on sustainability and patient well-being, the use of eco-friendly and biocompatible materials will become paramount. As telemedicine becomes an integral part of healthcare delivery, the need for remote monitoring devices will rise. Custom medical electrodes with the capability to transmit data seamlessly will be in high demand, and Screentec’s innovation in printed electronics aligns perfectly with this trend. Custom medical electrodes manufactured on textiles offer improved comfort, making continuous monitoring more patient-friendly. Moreover, this trend aligns with the growing importance of patient experience in healthcare solutions.
In the dynamic landscape of medical technology, where innovation and feasibility are inseparable companions, navigating the complex path from concept to reality is a formidable challenge. As a MedTech company specializing in contract development and manufacturing of custom medical electrodes, Screentec thrives in meeting and exceeding these demands, showcasing a proven ability to bring ideas to fruition.
Screentec has a rich history in the field of printed electronics, making them experts in their craft. Years of working in close connection with material suppliers have helped us curate a broad material library, ensuring an extensive know-how on the latest and best suited materials for our customers’ products. With a full range of capabilities from prototype to mass manufacturing, Screentec is uniquely positioned to forge the world of custom medical electrodes and rapid diagnostics.
Join us on this journey from innovation to product as we uncover the crucial role of feasibility studies, the power of customization, the impact of wearable technology, and the latest advancements in the field of printed electronics.
Can a concept become a real, practical, and cost-effective solution for healthcare?
The journey begins with a comprehensive understanding of the technology and materials available. Over the years, Screentec has consistently demonstrated their expertise in transforming innovative ideas into tangible, high-quality products that meet customers’ needs and expectations.
Screentec understands the critical importance of feasibility at every stage of development, from the prototype phase to mass manufacturing. Our journey in product development has been marked by a commitment to innovation and a deep understanding of the demands of the healthcare industry. This experience has not only refined our processes, but also allowed us to continuously adapt and stay at the forefront of industry trends. The good results we have achieved are a testament to our dedication to delivering high quality solutions.
Customization is Key: In the realm of disposable medical electrodes, customization is essential to meet the unique needs of each customer. Custom medical electrodes created through printed electronics technology find applications in various fields: they can be tailored for specific monitoring applications, such as ECG for cardiac health, EEG for brain activity, or EMG for muscle performance, to name a few. Screentec, with its adeptness in tailoring products according to specific applications, boasts a powerful advantage in this domain.
Integration with Wearable Devices: The integration of printed electronics into wearable devices complements point-of-care diagnostics by offering continuous monitoring capabilities. This connectivity allows for real-time data collection and transmission, enabling healthcare professionals to make informed decisions promptly.
The Power of Printed Electronics
The application of printed electronics is a game-changer in custom disposable medical electrodes and rapid diagnostics. It offers flexibility, precision, and scalability, making it a perfect fit for MedTech innovations. Printed electronics allow for intricate circuit designs and lightweight, conformable electrode shapes. These electrodes can be designed to fit the exact needs of different diagnostic or monitoring applications. Having a vast material library, on the other hand, empowers Screentec to select the ideal materials for each project, ensuring that feasibility is never compromised. With the right materials, these custom disposable medical electrodes can maintain the highest standards of quality and reliability.
Scalability: Scalability is where the rubber meets the road. Here, the feasibility of taking a product from concept to mass production is realized. Screentec’s comprehensive in-house capabilities and its ability to access the right materials make it possible to scale up efficiently without compromising on quality, whether we are producing a small batch or large quantities of electrodes.
Product-Specific Assembly Line: For large production volumes, it is essential to have a product-specific assembly line to maintain affordable processing costs. Having a dedicated assembly line promotes consistency in the manufacturing process, which is critical for maintaining product quality and meeting regulatory standards.
Vertical Integration for Full Manufacturing Control: Screentec prides itself on vertical integration, which means we handle most of the manufacturing phases in-house. This end-to-end approach allows us to maintain full control over every aspect of the production process. From materials sourcing to design, prototyping and mass manufacturing, until final assembly and packaging, we have the capabilities to ensure quality, efficiency, and innovation at every stage. Vertical integration enables us to meet and exceed the expectations of our clients while maintaining strict quality standards.
Impact of Process Validation on Quality
Process validation is a critical element in the production of printed electronics for medical electrodes. It ensures that the manufacturing process is well-defined, controlled, and capable of consistently producing high-quality products. This, in turn, contributes to the overall reliability, efficiency, and regulatory compliance of the manufacturing process.
Validated process is a reliable process. Process validation ensures that the manufacturing process is consistent over time. This consistency is essential for meeting regulatory requirements and maintaining product quality from batch to batch. By identifying and mitigating potential sources of variation, the likelihood of defects or failures in the final product is minimized, enhancing overall reliability. Validating the process also allows for optimization and streamlining of operations. Efficient processes are not only cost-effective but also contribute to the overall quality by reducing the chances of errors and variations.
In industries such as medical devices, adherence to regulatory standards is paramount. Process validation provides the necessary evidence to demonstrate compliance with regulatory requirements, ensuring that products meet the specified standards for safety and efficacy.
Printed Electronics in Point-of-Care Diagnostics
Point-of-care diagnostics, another specialty of the company with its emphasis on swift and accurate medical testing near the patient, greatly benefits from the innovative features and scalability offered by printed electronics. The application of printed electronics technology enhances the efficiency of rapid diagnostics in several ways:
Flexibility and Adaptability: Printed electronics allow for the creation of flexible and adaptable diagnostic devices. This flexibility is crucial in designing portable and user-friendly point-of-care diagnostic tools that can be easily integrated into various healthcare settings. The adaptability of printed electronics ensures that diagnostic devices can conform to different form factors and be tailored to specific testing requirements.
Cost-Effectiveness: Printed electronics offer a cost-effective solution to produce diagnostic devices. The adoption of cost-effectiveness evolves throughout the development lifecycle of printed electronics for diagnostic devices. The prototype phase allows for experimentation and proof of concept, while the production phase shifts focus towards achieving scalability, material cost optimization, process efficiency, and quality assurance to deliver cost-effective solutions on a large scale.
Customization for Specific Tests: The innovative nature of printed electronics allows for the customization of diagnostic devices to target specific tests and applications. This tailoring capability ensures that point-of-care diagnostic tools can address a diverse range of medical conditions, making them versatile and applicable across various healthcare scenarios.
In summary, the innovation and scalability of printed electronics enhance point-of-care diagnostics by providing flexible, cost-effective, customizable, and integrated solutions. These advancements contribute to the development of efficient diagnostic tools that play a crucial role in improving healthcare outcomes at the point of need.
Collaboration and Communication
Collaboration is the key to success. By working closely with clients and partners, and involving them in the production process, we ensure that feasibility is not just a box to be checked, but a dynamic, ongoing dialogue. Screentec has a well-established contact network, and a significant part of this network involves our active participation as a member of the PrintoCent cluster. The PrintoCent Industry Cluster (PIC) is a community comprised of approximately 40 members, including start-ups, SMEs, and large-scale industrial companies as well as research institutes from around the world. The cluster members are global industrial companies representing different parts of the value chain, enabling the commercialization of new products and services. Through our affiliation with PIC, we have access to a vast pool of expertise, resources, as well as cutting-edge technologies. This collaborative environment allows us to stay updated on the latest industry trends and developments, fostering innovation in our solutions.
In line with our commitment to collaborative advancements, Screentec has also joined forces with VTT and MedPhab Pilot Line. MedPhab, a consortium of partners from leading research centers and industrial players in medical devices and photonics, accelerates the development of photonic devices for medical applications, expediting the “idea to product” pathway. The latest manifestation of our collaboration is the joint demonstrator by Screentec and VTT. This non-invasive, skin-adherent PPG sensor is meticulously designed from a flexible and skin-friendly adhesive on TPU, specializing in optical heart rate monitoring through advanced technology.
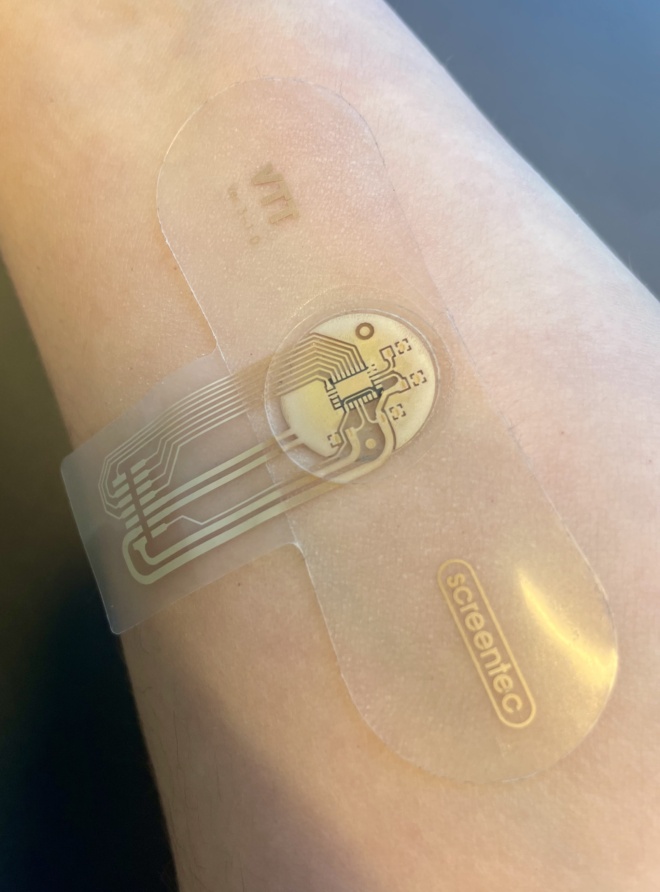
Heart rate skin patch sensor with VTT
The Latest Advancements in the Field of Printed Electronics – The Path Forward
And what does the future hold for Screentec? In the world of development of custom medical electrodes and rapid diagnostics, feasibility is not just a concept, it’s a way of life. It is a journey that begins with experience, is fueled by innovation, and thrives on collaboration. Screentec, with its extensive know-how on printed electronics, materials, and processes, has set a high standard for product development. The company’s drive to propel textile printing forward, commitment to sustainability, and continuous exploration of state-of-the-art technologies position it as a dynamic contributor sculpting the future of medical technology.
Stay tuned as we dive into these topics in our following blog posts. Meanwhile, you may want to get acquainted with Screentec’s latest projects and broad collaboration network: